What is Porosity in Welding: Recognizing Its Reasons and Enhancing Your Skills
The Scientific Research Behind Porosity: A Comprehensive Overview for Welders and Fabricators
Recognizing the detailed devices behind porosity in welding is crucial for welders and producers aiming for impressive craftsmanship. As metalworkers explore the midsts of this sensation, they reveal a world controlled by different aspects that affect the formation of these small voids within welds. From the composition of the base materials to the details of the welding process itself, a wide variety of variables conspire to either exacerbate or ease the visibility of porosity. In this extensive guide, we will certainly unravel the science behind porosity, discovering its effects on weld quality and introduction advanced strategies for its control. Join us on this journey via the microcosm of welding imperfections, where accuracy meets understanding in the quest of perfect welds.
Understanding Porosity in Welding
FIRST SENTENCE:
Examination of porosity in welding reveals essential insights into the stability and quality of the weld joint. Porosity, identified by the existence of tooth cavities or gaps within the weld metal, is a common concern in welding procedures. These gaps, otherwise correctly attended to, can compromise the structural integrity and mechanical residential or commercial properties of the weld, leading to potential failings in the finished product.

To find and measure porosity, non-destructive screening methods such as ultrasonic screening or X-ray inspection are often employed. These techniques allow for the recognition of interior problems without compromising the honesty of the weld. By examining the dimension, shape, and distribution of porosity within a weld, welders can make enlightened choices to improve their welding procedures and accomplish sounder weld joints.
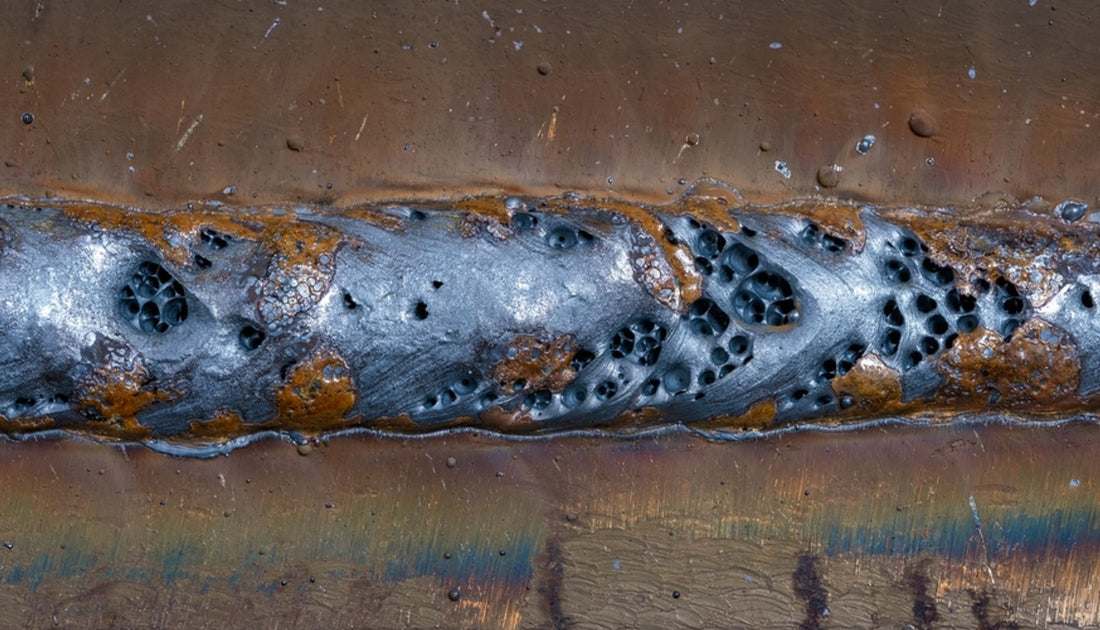
Elements Influencing Porosity Formation
The incident of porosity in welding is affected by a myriad of aspects, varying from gas shielding efficiency to the details of welding parameter settings. Welding specifications, consisting of voltage, present, take a trip speed, and electrode type, additionally influence porosity formation. The welding method used, such as gas steel arc welding (GMAW) or protected steel arc welding (SMAW), can affect porosity formation due to variations in warm circulation and gas coverage - What is Porosity.
Effects of Porosity on Weld High Quality
Porosity development considerably jeopardizes the architectural honesty webpage and mechanical homes of bonded joints. When porosity exists in a weld, it develops voids or tooth cavities within the product, reducing the general strength of the joint. These gaps serve as anxiety focus points, making the weld extra at risk to cracking and failure under load. The presence of porosity likewise deteriorates the weld's resistance to rust, as the entraped air or gases within deep spaces can respond with the surrounding setting, leading to degradation with time. Additionally, porosity can hinder the weld's ability to endure pressure or impact, further threatening the general high quality and reliability of the welded structure. In crucial applications such as aerospace, automotive, or structural building and constructions, where security and toughness are vital, the damaging impacts of porosity on weld high quality can have severe effects, stressing the value of reducing porosity through correct welding methods and procedures.
Techniques to Decrease Porosity
In addition, using the appropriate welding specifications, such as the right voltage, existing, and take a trip rate, is crucial in avoiding porosity. Preserving a regular arc size and angle throughout welding additionally assists decrease the likelihood of porosity.

In addition, choosing the right shielding gas and keeping weblink proper gas flow rates are important in reducing porosity. Using the suitable welding technique, such as back-stepping or employing a weaving motion, can likewise assist disperse warm uniformly and decrease the chances of porosity formation. Guaranteeing proper ventilation in the welding environment to get rid of any type of prospective sources of contamination is important for achieving porosity-free welds. By implementing these methods, welders can effectively reduce porosity and produce high-quality bonded joints.
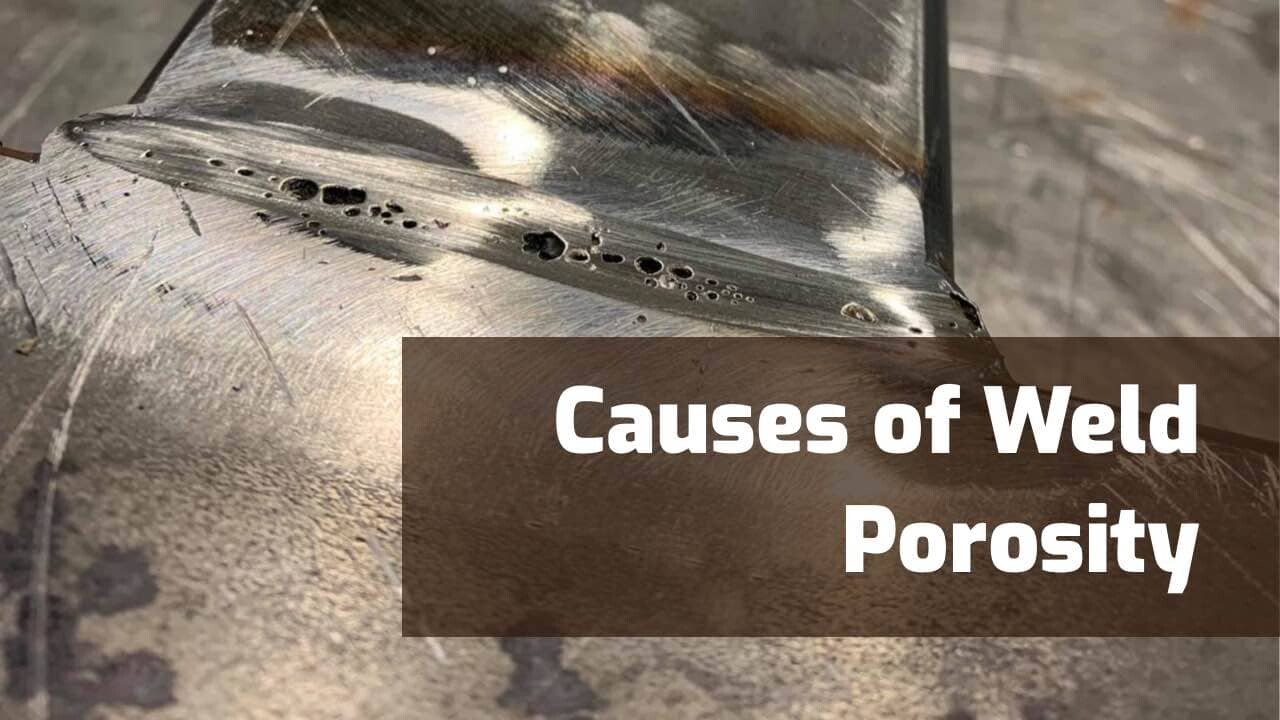
Advanced Solutions for Porosity Control
Carrying out sophisticated modern technologies and ingenious techniques plays a crucial function in accomplishing exceptional control over porosity in welding processes. One sophisticated service is using sophisticated gas mixtures. Securing gases like helium or a blend of argon and hydrogen can help lower porosity by offering better arc security and improved gas protection. In addition, utilizing sophisticated welding techniques such as pulsed MIG welding or changed environment welding can also aid alleviate porosity issues.
Another sophisticated solution includes making use of advanced welding equipment. Making use of equipment with integrated features like waveform control and sophisticated power sources can boost weld quality and minimize porosity threats. In addition, the implementation of automated welding systems with precise control over parameters can considerably reduce porosity issues.
Furthermore, incorporating innovative tracking and evaluation technologies such as real-time X-ray imaging or automated ultrasonic testing can assist in detecting porosity early in the welding process, enabling for prompt rehabilitative actions. Overall, integrating these sophisticated options can substantially improve porosity control and enhance the overall quality of recommended you read welded elements.
Final Thought
In final thought, understanding the scientific research behind porosity in welding is vital for welders and makers to create high-quality welds - What is Porosity. Advanced services for porosity control can further boost the welding procedure and make sure a strong and reliable weld.